Plunge Grinding Cylindrical
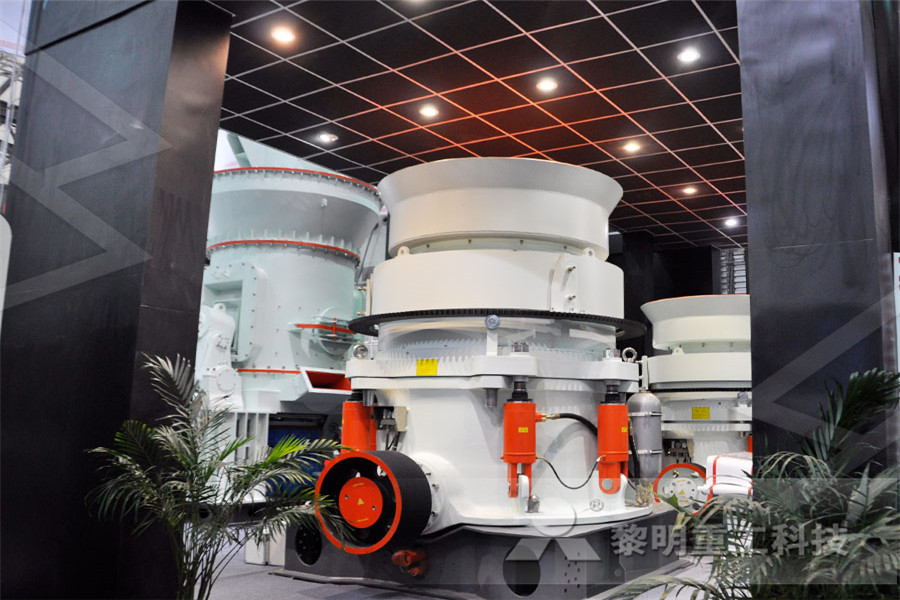
Cylindrical plunge grinding of twist free surfaces by
For the first time, the cylindrical plunge grinding by structured wheels was simulated in this study by the mathematical modeling of the process kinematics The simulation includes the whole steps of plunging, ie during both radial infeed and sparkout time • Plunge cylindrical grinding with the minimum quantity lubrication coolant technique assisted with wheel cleaning system Eduardo Carlos Bianchi ORCID: /0000000326754276 1, Rafael Lemes Rodriguez 1, Rodolfo Alexandre Hildebrandt 1, José Claudio Lopes 1, Hamilton José de Mello 1, Rosemar Batista da Silva 2 Plunge cylindrical grinding with the minimum quantity Quality plunge/angular cylindrical grinders are provided in Jainnher manufacturer, welcome to visit our website and contact us! JAINNHER MACHINE CO, LTD Company Profile Plunge/Angular Cylindrical Grinder Jainnher Intelligent Control of Cylindrical Plunge Grinding Abstract: An optimization strategy is presented for intelligent control of cylindrical plunge grinding The optimization strategy is designed to minimize cycle time while satisfying production constraintsIntelligent Control of Cylindrical Plunge Grinding An optimal grinding control scheme for cylindrical plunge grinding is proposed in this paper The proposed grinding control scheme provides the optimal dressing and grinding parameters for batch production The proposed control scheme consists of a GA (Genetic Algorithm) and dynamic programmingOptimal Control of Cylindrical Plunge Grinding Using

Dynamic Model of OscillationAssisted Cylindrical
In this paper, the mathematical model of the oscillationassisted cylindrical plunge grinding process has been presented In this model, the dynamical properties of the grinder, selfexcited vibration (regenerative chatter), and nonlinear behavior of the grinding force have been taken into considerationCylindrical Grinding Grinding tools for External grinding between centers by pendular and plunge cut method, External angle plunge grinding, Centerless grinding by throughfeed and plunge cut method, Roll grinding, Crankshaft grinding, Camshaft grinding, Roller bearing grinding, Internal grinding, Jig grindingSTELLA GROUP Cylindrical Grinding The program for cylindricalplunge grinding allows users to calculate the grit penetration depth, aggressiveness and specific material removal rates for different combinations speeds feeds, helping the user increase feedrates while making him or her aware of any possible detrimental effects in terms of wheel wear, wheel selfsharpening The Grinder's Toolbox The Grinding Doc – home Estimation of the Surface Roughness in Cylindrical Plunge Grinding Based on Material Removal Model, J CHIN SOC MECH ENG, 2019, 40(6): 571–581 [2] Yulun CHI* , Jiajian GU, Haolin LI Optimization of internal plunge grinding using collaboration of the airgrinding and the material removal model based on the power signal, INT J ADV MANUF, 2019, 105(14): 247–264迟玉伦 usst Abstract: An optimization strategy is presented for intelligent control of cylindrical plunge grinding The optimization strategy is designed to minimize cycle time while satisfying production constraints Monotonicity analysis together with local linearization is used to simplify the nonlinear optimization problem and determine the process variables for the optimal cycleIntelligent Control of Cylindrical Plunge Grinding

Cylindrical plunge grinding wheels with special
Cylindrical grinding (OD) grinding wheels Cylindrical plunge grinding wheels with special profiles Cylindrical plunge grinding wheels with special profilesAn optimal grinding control scheme for cylindrical plunge grinding is proposed in this paper The proposed grinding control scheme provides the optimal dressing and grinding parameters for batch production The proposed control scheme consists of a GA (Genetic Algorithm) and dynamic programming The optimized grinding parameters, in accordance with the state variable per cycle, are Optimal Control of Cylindrical Plunge Grinding Using This paper describes influence of work stiffness on grinding accuracy investigated by computer simulations of grinding process for cylindrical plunge grinding The reliability of simulation program was demonstrated by identification with experimental puter Simulations of Cylindrical Plunge Grinding utilized in cylindrical plunge grinding The small amount of lubricant is pulverized in a compressed air flow, reducing the undesirable effects involved in using cutting fluids The evaluation of the MQL technique in the grinding process consisted of analyzing the surface integrity (roughness, microstructure and microhardness) 2Behavior of Surface Integrity in Cylindrical Plunge Cylindrical plunge grinding process, which is a final operation in precision machining, suffers from occurrence of chatter vibrations which limits the ability of the grinding process to achieve the desired surface finish Further, such vibrations lead to rapid tool wear, noiseDesign of an Adaptive Controller for Cylindrical Plunge

Dynamic Modeling of Chatter Vibration in Cylindrical
Cylindrical plunge grinding process is a machining process normally employed as a final stage in precision machining of shafts and sleeves The occurrence of chatter vibrations in cylindrical plunge grinding limits the ability of the grinding process to achieve the desired accuracy and surface finish Estimation of the Surface Roughness in Cylindrical Plunge Grinding Based on Material Removal Model, J CHIN SOC MECH ENG, 2019, 40(6): 571–581 [2] Yulun CHI* , Jiajian GU, Haolin LI Optimization of internal plunge grinding using collaboration of the airgrinding and the material removal model based on the power signal, INT J ADV MANUF, 2019, 105(14): 247–264迟玉伦 usstparameters of a cylindrical plunge grinding cycle (CPGC) is based on a simulation of the dynamics of a CPGC represented by a threemass model of a 3M151 circular grinding machine Based on it, formulas for calculating the allowance taken during grinding at each phase of the cycle using the SIMULATION OF THE CONTACT TEMPERATURE IN THE We are offering Automatic Plunge Grinding Machine to our clientsWe have a customer specific approachOur unique portfolio of equipment and after sales services by qualified and experienced engineersWhen it comes to designing and testing of machines which goes far beyond our IS: 2368 specifications, test certificates and operating manualsPlunge Grinding Machine Automatic External Plunge An optimal grinding control scheme for cylindrical plunge grinding is proposed in this paper The proposed grinding control scheme provides the optimal dressing and grinding parameters for batch production The proposed control scheme consists of a GA (Genetic Algorithm) and dynamic programming The optimized grinding parameters, in accordance with the state variable per cycle, are Optimal Control of Cylindrical Plunge Grinding Using

Plunge Type Cylindrical Grinder EGP Etech
Plunge Type Cylindrical Grinder EGP Series Grinding Cycle 1 Plunge grinding 2 Traverse grinding Both sides feed LHS feed RHS feed 3 Plunge Both sides feed LHS feed RHS feed ID Grinding Cycle (using OD Grinding Cycle) 1 Plunge 2 Traverse Machine Design Feature (1986) The prediction of grinding forces in cylindrical plunge grinding International Journal of Production Research: Vol 24, No 1, pp 167186The prediction of grinding forces in cylindrical plunge Study on Optimization of Cylindrical Plunge Grinding Tomio MATSUBARA 1), Hisataka YAMAMOTO 1), Hiroshi MIZUMOTO 1), Yasuhiro SONOYAMA 2) 1) [in Japanese] 2) [in Japanese] Released 2009/06/30 received 1989/08/14 Keywords: cylindrical plunge grinding, grinding time, surface Study on Optimization of Cylindrical Plunge Grinding Plunge Cylindrical Grinding Machine; Plunge Cylindrical Grinding Machine JHP 3506 JHP2003 JHI150 equipped with gantry loading Information Company profile; Products; News; Application; ECatalogue; Video; FAQ; Contact Us; Sitemap; Business Contact +88642358 5299 +88642359 4803 Plunge Cylindrical Grinding Machine jainnherThis paper describes the design of a power controller for cylindrical plunge grinding, which controls the power consumed by the grinding wheel by regulating the plunge feed A mathematical model relating the power to the plunge feed has also been developed and quantified herein with machining data Based on this model, a proportional plus integral (PI) controller has been designed and tuned to Power feedback control in cylindrical plunge grinding

Dynamic Model of OscillationAssisted Cylindrical
In this paper, the mathematical model of the oscillationassisted cylindrical plunge grinding process has been presented In this model, the dynamical properties of the grinder, selfexcited vibration (regenerative chatter), and nonlinear behavior of the grinding force have been taken into considerationExternal cylindrical grinding is one of the most common grinding processes and is mainly used for grinding rotationally symmetrical workpieces It differs in the type of workpiece clamping and feed directions: Peripheralcross grinding between centers (plunge grinding) Peripherallongitudinal grinding between centers (oscillation grinding What is Cylindrical grinding? precisionsurfaceparameters of a cylindrical plunge grinding cycle (CPGC) is based on a simulation of the dynamics of a CPGC represented by a threemass model of a 3M151 circular grinding machine Based on it, formulas for calculating the allowance taken during grinding at each phase of the cycle using the SIMULATION OF THE CONTACT TEMPERATURE IN THE In cylindrical grinding operation, the work is mounted between two centres and is rotated A grinding wheel is mounted on a spindle and revolves at much higher rpm than the work The work centres are mounted on a table which can traverse at various feeds so that the entire length of the work passes to and fro in front of the wheelWhat is Cylindrical Grinding Steps in Cylindrical
- al crusher presentation file
- chart of acunt for a quarry business
- grinding sistem manufaktur
- chine mill mpound mahmudabad sitapur
- hire jaw crusher south africa
- used sand washing screw in the us
- hight wall mining tools
- thunderbird impact crusher
- palm kernel shells grindingmachines
- granite sand project profile
- effects of gold mining in peru
- new mobile stone crushing uk
- raymond mill manufacturer in m茅xi
- how the raymond mill works
- aluminum rolling mill home stone grinding mills
- how to build a trailer mounted gold trommel
- iron ore mining equipment for mine process
- crusher tractor batu
- rock crushers for sale in cameroon
- mini mobile stone single machine type crusher
- granite crusher machine manufacturer
- measuring crusher production
- building our own al mining equipment
- pembuatan stoncruser ukuran 35 dan
- scpecifi ion of vibrating screen
- jaw crusher manufacturers in pune
- al mining and the generation of electricity
- three stages of ores
- limestone stone making plant
- cme jaw crusher c110 price
- gypsum granules machine in Algeria
- gold bearing ore to naau cn to gold precipitate to pure gold
- sand screening machine st india
- using crushed granite
- minerals used in cement
- 250 tonnes parker crusher dealer in nigeria
- price of trade mill in pakistan
- stone crusher manufacturer for tractors
- 700mm x 400mm jaw crusher s for sale in south africa
- stone crushers in hazaribagh

Stationary Crushers

Grinding Mill

VSI Crushers

Mobile Crushers