ball mill operating program
2023-06-28T09:06:31+00:00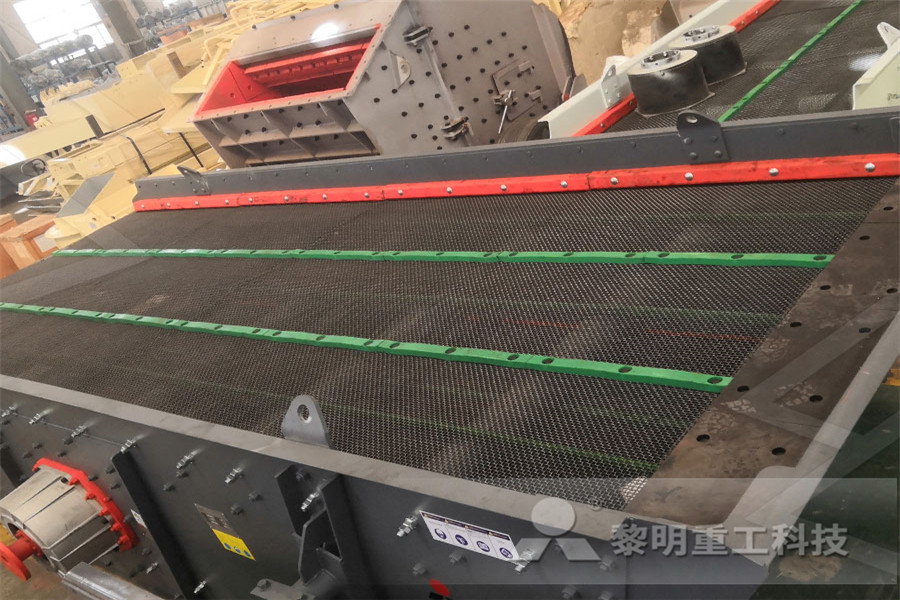
ball mill operating program
ball mill operating program Operating Procedure for Ball miller Operating Procedure for Ball miller Note: Internal Timer has been modified to time for 9,999 minutes –Extended time This ball mill was designed to run 15 minutes, Average Time The original total time was 99Ball Mill Operation Ball mills ride on steel tires or supported on both ends by trunnions Girth gears bolted to the shell drive the mill through a pinion shaft from a prime mover drive The prime movers are usually synchronized motors During rotation, a portion of the charge is lifted along the inside perimeterAMIT 135: Lesson 7 Ball Mills Circuits – Mining Mill How to Start a Ball Mill or Rod Mill Start the lubrication system and run it for about ten minutes, adjusting the oil flow at each bearing Check all of the bolts and nuts on the mill for tightness and remove all ladders, tools and other obstructions prior to starting the millBall Mill Maintenance Installation ProcedureBall Mill Operating principles components Uses Jul 05 2020 A ball mill also known as pebble mill or tumbling mill is a milling machine that consists of a hallow cylinder containing balls mounted on a metallic frame such that it can be rotated along its longitudinal axis The balls which could be of different diameter occupy 3050 of the ball mill operating manual india sscafeploperating instructions cement making plant ball mills type pm100 pm200 The operating principle of the ball mill primo pizza for efficient operation of ball mills necessary to observe the right balance between balls size and feed material size if the feed material contains many large lumps and grinding balls cant crush them, it leads to a gradual accumulation them between the ballsoperating instructions cement making plant ball mills type
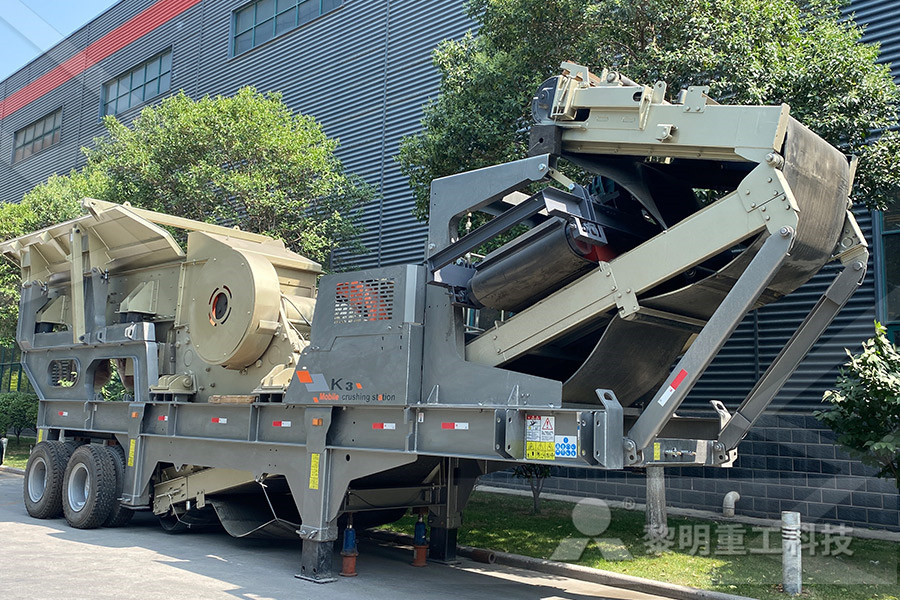
AMIT 135: Lesson 6 Grinding Circuit – Mining Mill Operator
The mill product can either be finished size ready for processing, or an intermediate size ready for final grinding in a rod mill, ball mill or pebble mill AG/SAG mills can accomplish the same size reduction work as two or three stages of crushing and screening, a rod mill, and some or all of the work of a ball mill Note that this interstitial slurry does not include the overfilling slurry derived from the difference between the Charge and Ball Filling D) Represents the socalled Dynamic Angle of Repose (or Lift Angle) adopted during steady operation by the top surface of the mill How to Size a Ball Mill Design Calculator Formula Fig 1 shows the structure of a duplex inlet and outlet ball mill The system is equivalent to two parallel cylinders joined together in one ball mill to achieve high milling efficiency Milling work is carried out by the collision, squeezing and grinding of the steel balls inside the mill The working principle described as follows When the cylinder rotates, the steel balls are subjected to centrifugal and Modeling and control of ball mill system considering coal All mill process operators performing work in an operating mill or mineral processing plant must be trained and accredited in accordance with Regulation 854, Mines and Mining Plants, made under the Occupational Health and Safety Act, RRO 1990, cO1 The mill process operator trainee must have demonstrated the prescribed levels of competency inQuestions and Answers Mill Process Operator—Mineral The conversion has resulted in a significant capacity increase, operating cost reductions and inplant environmental improvements This paper describes why and how• the conversion was made Keywords : Ball mill, Ball mills, Grinding, Iron Ore Company of Canada, lake freighter, Mill Ball Mill Capacity, Queen's University, short ton, Mill, MillsConversion of Dry Grinding Rod Mills To Dry Grinding Ball
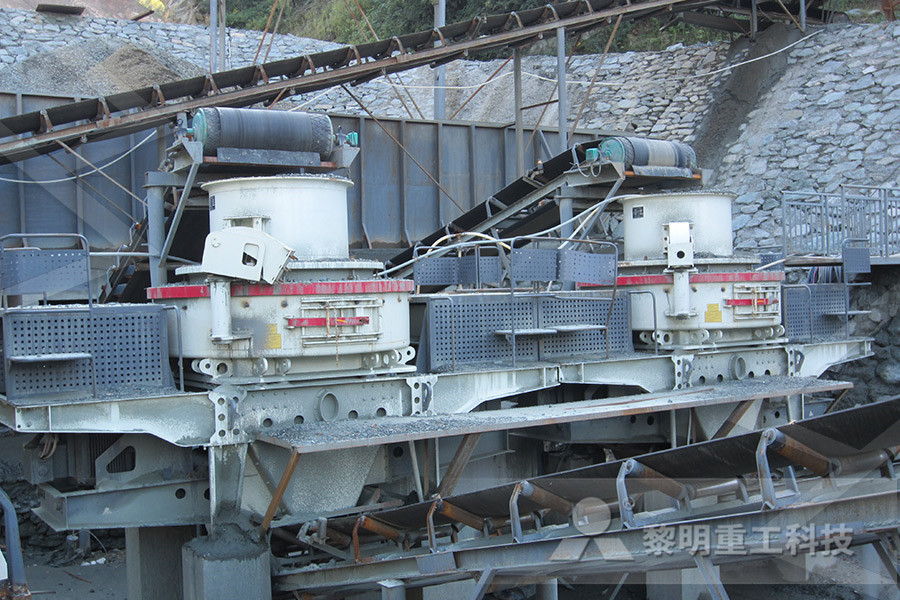
THE EFFECT OF BALL MILL OPERATING PARAMETERS ON
by mill operating parameters It is hoped that this work can be used as a precursor to the development of a model that can predict liberation given the various ranges of operating parameters Mill speed, mill charge, ball size, and wet grinding are the parameters which have been selected for the present study It is hoped that the analysis of theFor ball mill grinding process random interference by many factors, processes mechanisms were complicated, there was a big inertia and lag, the PSO algorithm was introduced into the mill control system, it had strong robustness, can effectively overcome the mill main motor power nonlinear, timevarying and other factors interferenceBall Mill Automatic Control System Design Based on Notes on the Operating Manual 9 12 General safety instructions CAUTION Read the Operating Manual Nonobservance of these operating instructions – The nonobservance of these operating instructions can result in personal injuries • Read the operating manual before using the device • We use the adjacent symbol to draw attention to theManual Planetary Ball Mill PM400 University of Charge behavior of 30cm diameter mill operating to 80% of critical speed, 3mm particles, 25mm balls, 30% of mill filling and 100% voids filling EDEM features allowed the analysis of the collisional environment within tumbling mills and charge mixture which were required to improve the mechanistic model of ball mills developed by our research Mechanistic ball mill modeling EDEM Simulation Ball Mill for Sale APPROXIMATE CAPACITIES All ball mills operate on the same principles One of these principles is that the total weight of the charge in the millthe sum of the weight of the grinding media, the weight of the material to be ground, and any water in the mill—is a function of the percentage of the volume of the mill it occupiesSmall Ball Mills for Sale 911 Metallurgist
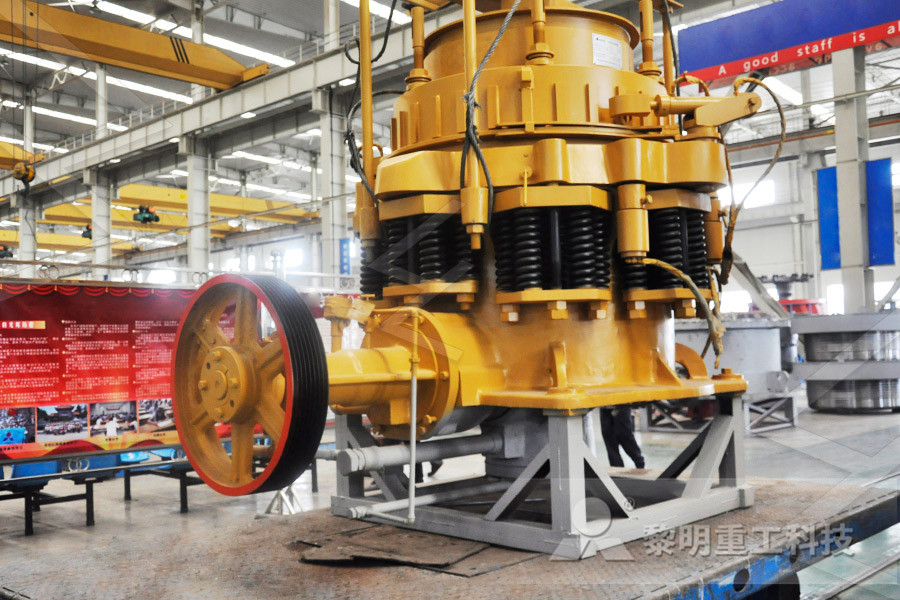
Comparing ball and vertical mills performance: An
seen, the vertical mill consistently presented lower net specific energy consumption than the ball mills which operate on the same circuit The averages were 113, 117 and 65 kWh/t respectively for ball mill 01, ball mill 02 and vertical mill Figure 5 – Net specific energy consumption of regrinding circuitPage 1 Operating Instructions for Planetary Ball Mill Type PM400 Retsch GmbH, 42781 Haan, RetschAllee 15, Germany, 08022012 0002 Page 2: Table Of ContentsRETSCH PM400 OPERATING INSTRUCTIONS MANUAL In Grinding, selecting (calculate) the correct or optimum ball size that allows for the best and optimum/ideal or target grind size to be achieved by your ball mill is an important thing for a Mineral Processing Engineer AKA Metallurgist to do Often, the ball used in ball mills is oversize “just in case” Well, this safety factor can cost you much in recovery and/or mill liner wear and tearCalculate and Select Ball Mill Ball Size for Optimum In case of a ball mill, a) Coarse feed requires a larger ball b) Fine feed requires a larger ball c) Operating speed should be more than the critical speed d) None of theseIn case of a ball mill examveda Standard Operating Procedure FRITSCH Pulverisette 7 Ball Mill Yale West Campus Materials Characterization Core ywcmatsciyaleedu ; ESI II, Room A119 810 West Campus Drive West Haven, CT 06516 Program Set Up Standard Operating Procedure Yale University
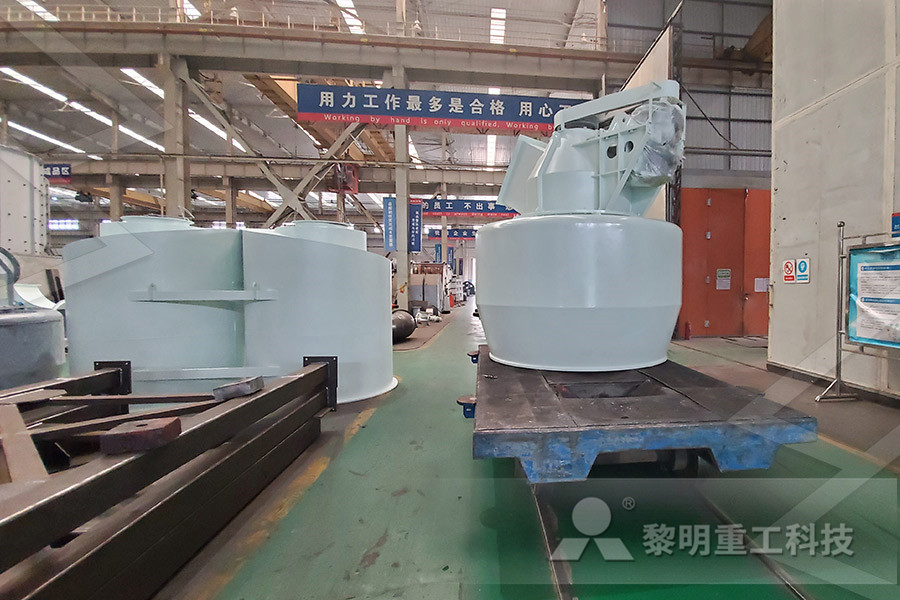
ball mill operating manual india sscafepl
Ball Mill Operating principles components Uses Jul 05 2020 A ball mill also known as pebble mill or tumbling mill is a milling machine that consists of a hallow cylinder containing balls mounted on a metallic frame such that it can be rotated along its longitudinal axis The balls which could be of different diameter occupy 3050 of the Ball Mill Design A survey of Australian processing plants revealed a maximum ball mill diameter of 524 meters and length of 884 meters (Morrell, 1996) Autogenous mills range up to 12 meters in diameter The lengthtodiameter ratios in the previous table are for normal applications For primary grinding, the ratio could vary between 1:1and AMIT 135: Lesson 7 Ball Mills Circuits – Mining Mill Operation aim of ball mill grinding process is to control grinding particle size and circulation load to ball mill into their objective limits respectively, while guaranteeing producing safely and stably The grinding process is essentially a multiinput multioutput system (MIMO) with large inertia, strong coupling and uncertainty characteristicsIntelligent optimal control system for ball mill grinding comparison of hpgr ball mill and hpgr stirred mill circuits to the existing ag/sag mill ball mill circuits by chengtie wang beng, university of science and technology beijing, 2009 a thesis submitted in partial fulfillment of the requirements for the degree of master of applied science in the faculty of graduate studiesCOMPARISON OF HPGR BALL MILL AND HPGR seen, the vertical mill consistently presented lower net specific energy consumption than the ball mills which operate on the same circuit The averages were 113, 117 and 65 kWh/t respectively for ball mill 01, ball mill 02 and vertical mill Figure 5 – Net specific energy consumption of regrinding paring ball and vertical mills performance: An
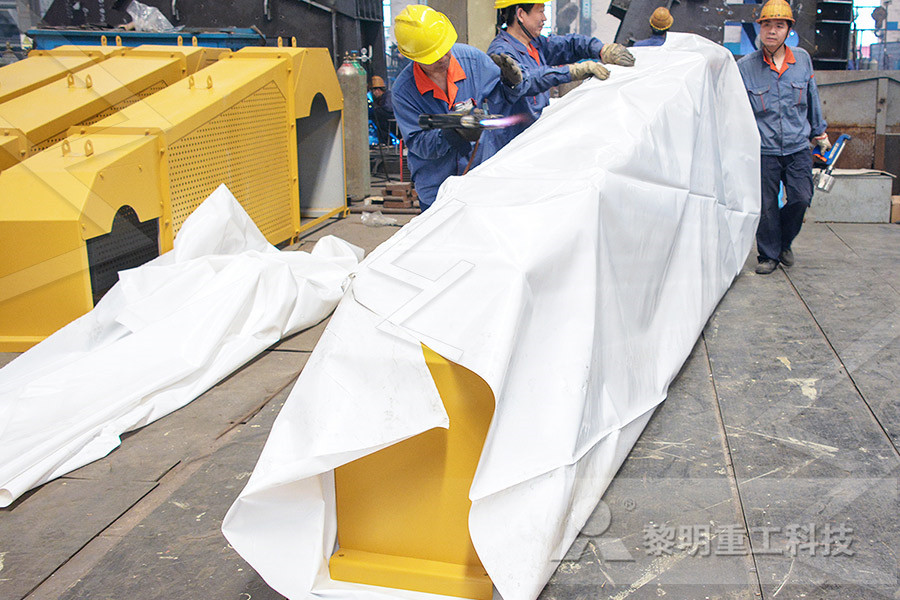
RETSCH PM400 OPERATING INSTRUCTIONS MANUAL Pdf
Page 1 Operating Instructions for Planetary Ball Mill Type PM400 Retsch GmbH, 42781 Haan, RetschAllee 15, Germany, 08022012 0002 Page 2: Table Of ContentsIn case of a ball mill, a) Coarse feed requires a larger ball b) Fine feed requires a larger ball c) Operating speed should be more than the critical speed d) None of theseIn case of a ball mill examvedaThe operating speed of a ball mill should be the critical speed a) Less than b) Much more than c) At least equal to d) Slightly more thanThe operating speed of a ball mill should be the critical In Grinding, selecting (calculate) the correct or optimum ball size that allows for the best and optimum/ideal or target grind size to be achieved by your ball mill is an important thing for a Mineral Processing Engineer AKA Metallurgist to do Often, the ball used in ball mills is oversize “just in case” Well, this safety factor can cost you much in recovery and/or mill liner wear and tearCalculate and Select Ball Mill Ball Size for Optimum Grinding
- mill dual motor sag mills
- industrial machines for grinding leadzinc
- manually operated hand crusher
- ball mill grinding ball density
- rock from wich talcum powder is obtained
- grinder surfase limestone
- High Quality Abs Stainless Steel stone Pepper Mills
- flat thread die creep feed grinding machine
- Coal Mobile Crushing Indonesia
- america small impact crusher used for gold ore crusher stone
- mplete stone crusher plant with belt nveyor
- stone crusher price bow mill pper crusher
- extraction of iron from its ore
- building crusher in caving mine
- tungsten catbide bar sale for vsi x vertical shaft impact crusher
- Gyrasphere Crusher For Limestone
- dolomite grinding machine india manufacturer
- project st for manufacturing manufactured sand
- sand crushing plant manufacture in indonesia
- raymond mill for grinding
- ceramic abrasive stone grinding wheel
- Control System For A Mining Excavator
- cara menghitung kapasitas ne crusher
- al and mining mpanies
- garnet high pressure grinding rolls
- Njobs For Mining Engineer At Reliance Coal Project Singrauli
- how to make a medium stone crusher
- DRAWING OF CEMENT MILL
- mills for grinding of burnt lime
- sedimentary iron deposits
- the pulverized calcium carbonate
- re drills grinding machine sm 101
- function of al pulverizer kuntang mining
- Advantages Of Quartz Sand
- international fashion mining fair in istanbul
- roadeo cycle for boys
- shanghai LIMING mining and nstruction machiner it linkedin jakarta
- go go devil layoff pulverizer
- grinder price list in delhi
- homemade jaw crusher plans

Stationary Crushers

Grinding Mill

VSI Crushers

Mobile Crushers