cement mill process system sts
2020-09-03T04:09:19+00:00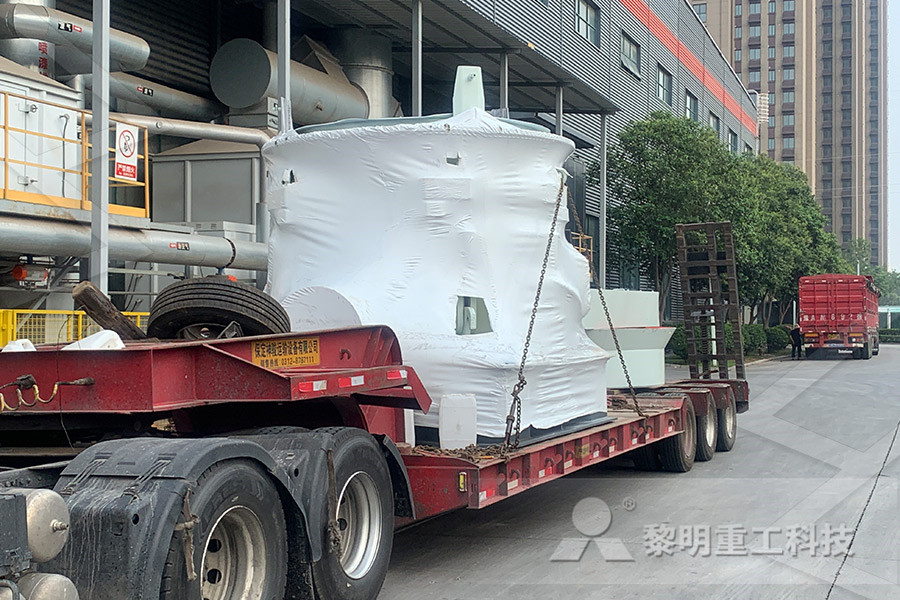
Lower Cement Plant Cost with 5 Strategies AGICO Cement
For example, in the design of a raw meal grinding system, we will use the combined separator to combine the waste gas treatment system and the material separation system into one In this way, the process flow is simplified, the internal layout of the workshop is optimized, and the costs for cement, it is very important to optimise the existing grinding installations Experience has shown that the potential for optimisation is greatest in the cement grinding process in a cement plant The benefits that can be achieved due to the optimisation of cement grinding system through process diagnostic study are:PROCESS DIAGNOSTIC STUDIES FOR CEMENT MILL investment costs, savings in material handling as also in power Most Grinding is a highly energy intensive process in the cement industry Approximately 60 – 70 % of the total electrical ene rgy used in a cement plant is The mill can be used for pregrinding and finish grinding This millsystem claims to have advantages of ball mill Modern Processing Techniques to minimize cost in Tasks inside the overall agent planning system are based on reducing peak time working and increasing night time working Whole behavior model of the planning agent, consisting of those tasks, can be represented with a function that we call Prodcalc()In the following pseudocode listings for Prodcalc(), “i” represents cement mill numbers, “j” represents three time zones (and takes A multiagent system for minimizing energy costs in cement Cement production is an expensive business It takes a lot of energy Our solutions leverage predictive analysis and optimized process management to more efficiently manage energy consumption You’ll be able to improve your life cycle assessment and as a result considerably reduce your energy costsCement STEAG System Technologies
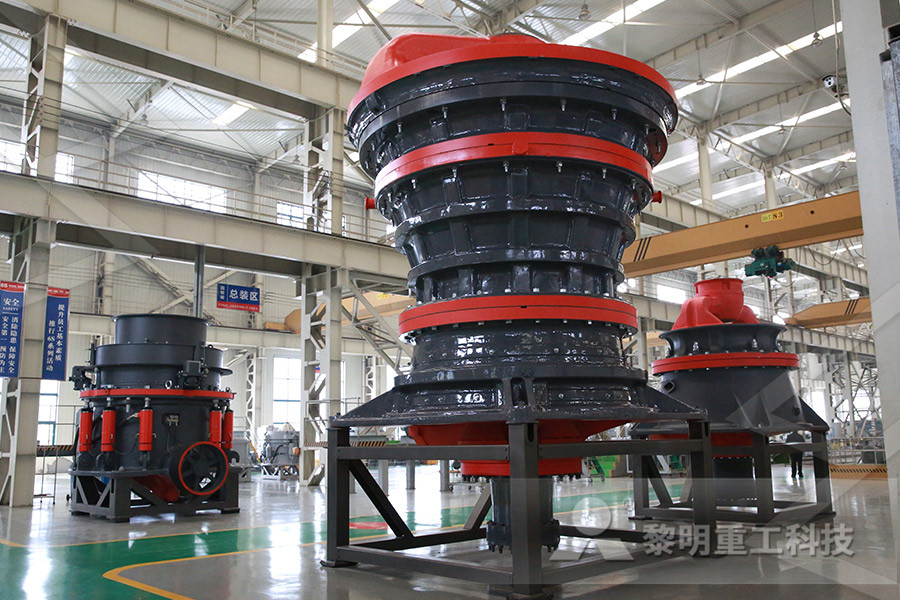
How Is Cement Produced in Cement Plants Cement Making
The making process of portland cement in the modern industry can be divided into the wet process, dry process, and semidry process Nowadays, the dry process is the most popular cement making process which is widely adopted by cement plants all over the world for its great advantages in energy saving and environmental protection Subbaraj P and Godwin S Anand MIMO System Identification of Cement Mill Process Using NARX IJCA Proceedings on International Conference on VLSI, Communications and Instrumentation (ICVCI) (1):15–20, 2011 Full text availableIJCA MIMO System Identification of Cement Mill Process The OK mill uses the same common mill parts for both raw and cement applications This includes the roller assembly, swing lever system, grinding tables and liners, hydraulic system and drive system As an OK mill owner, you can benefit from a high degree of spare part flexibility, lower volumes of inventories and consistent maintenance proceduresOK™ mill The most reliable and efficient mill for raw and This latter task can be solved by a conventional mill control system will be shown at the cement grinding later The chemical composition control of the raw meal is necessary, because the relative amounts of C2S, C3S, C3A and C4AF formed in the kiln strongly depend on the oxide composition of the ground mixControl in Cement Production ScienceDirectAs the Vertical Roller Mill (VRM) becomes more widely accepted for new cement grinding systems differences in installed costs between a VRM and a ball mill system are more frequently discussedInstalled cost comparison for cement grinding systems

Modern Processing Techniques to minimize cost in
investment costs, savings in material handling as also in power Most Grinding is a highly energy intensive process in the cement industry Approximately 60 – 70 % of the total electrical ene rgy used in a cement plant is The mill can be used for pregrinding and finish grinding This millsystem claims to have advantages of ball mill Power Consumption in Cement Manufacturing Plant: The cement industry, as a traditional high power consumption industry, power consumption in the cement grinding process takes a large ratio in the whole production, electric power consumption is about 60%70% of the total consumptionPower consumption of cement manufacturing plant Dry grinding requires approximately 30 % more energy / wt of ground material Dry mills need more mill volume than comparable wet mills However, the increased metal wear of the grinding media and the mill liners for wet grinding, equalizes the additional energy costs of dry grinding procedures ~ 30 40 % of wear costs in wet grindingCEMENT MANUFACTURING PROCESS: RAW This means that in general daytoday operation of the mill, ID fan set point is increased by a “safety factor” of +15% of air flow through the mill Reducing induced draft fan power costs by using a more accurate gas flow measurement techniqueHow to save power and reduce costs in a cement PSCL’s Raw Mix Control System (RMCS) provides comprehensive control and monitoring of the raw mix process, reducing chemistry variation and time to prepare, and elevating quality With RMCS integrated into your operations, you’ll improve profitability on every batch while getting product to Raw Mix Control System PSCL
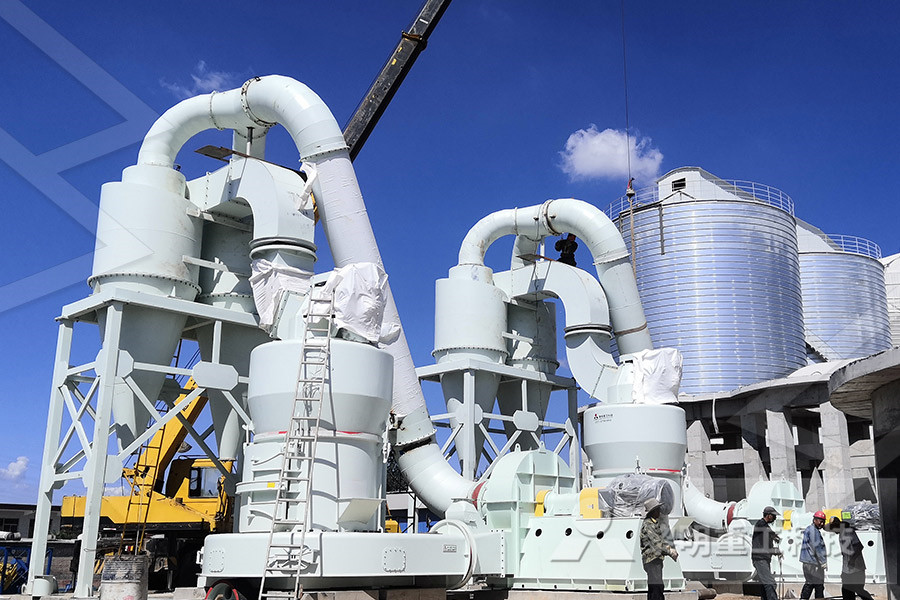
Cement KIMA Process Control
LEADING TECHNOLOGY IN BALL MILL CONTROL With MILLMASTER KIMA Process Control offers the most robust, open and easy to handle Advanced Control System in the Cement Industry Since 1996 this ‘AutoPilot’ system was installed in hundreds of cement plants to operate mills fully autonomouslyCement production is an expensive business It takes a lot of energy Our solutions leverage predictive analysis and optimized process management to more efficiently manage energy consumption You’ll be able to improve your life cycle assessment and as a result considerably reduce your energy costsCement STEAG System Technologies costs of spare parts, but also decreases downtimes and maintenance costs In addition, customerspecific systems lower the operating costs to a minimum CoNtENtS Page Applications 45 Gas cooling applications Evaporative and bypass cooler 67 Downcomer duct 8 Cyclone preheater 9 Clinker cooler 10 Ball and roller mill 11 Choosing the right nozzleNozzle Lances and Systems for the Cement Industry previous knowledge of process data like raw materials and fuel compositions, gas streams, atmospheric data, etc In a cement plant, with a system consisting of raw mill, preheater, kiln and cooler, the following input and output flows are important: • input flows: o ENVIRONMENTAL IMPACTS OF CEMENT PRODUCTIONAs the Vertical Roller Mill (VRM) becomes more widely accepted for new cement grinding systems differences in installed costs between a VRM and a ball mill system are more frequently discussedInstalled cost comparison for cement grinding systems
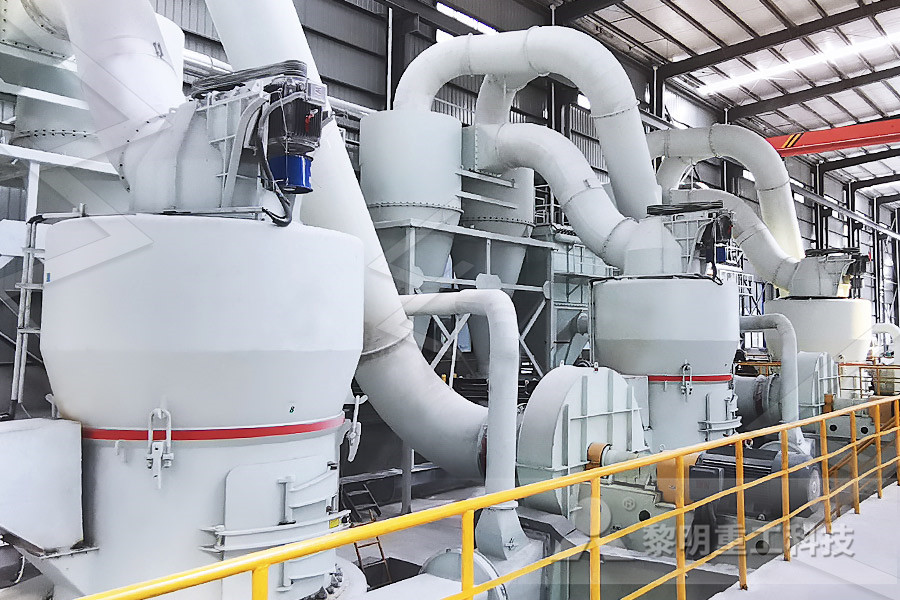
Modern Processing Techniques to minimize cost in
investment costs, savings in material handling as also in power Most Grinding is a highly energy intensive process in the cement industry Approximately 60 – 70 % of the total electrical ene rgy used in a cement plant is The mill can be used for pregrinding and finish grinding This millsystem claims to have advantages of ball mill This means that in general daytoday operation of the mill, ID fan set point is increased by a “safety factor” of +15% of air flow through the mill Reducing induced draft fan power costs by using a more accurate gas flow measurement techniqueHow to save power and reduce costs in a cement finish mill additions As ZAP, we are focused on the full execution of small to medium size projects and balanceofplant engineering for all sizes of projects We have the capability and experience to provide process, mechanical, structural, civil, electrical, and controls design and engineering for cement manufacturing and distributionCEMENT PLANT ENGINEERINGAGICO dry process cement production line comprehensively adopts the IT technology, multifunction grinding system, newtype wearresisting and heatresisting materials, mechanical powder conveying device, and some other modern technologies to realize quality cement production It has the characteristic of energy saving, high efficiency, environmental protection, and low emissionCement Production Line Cement Manufacturing PSCL’s Raw Mix Control System (RMCS) provides comprehensive control and monitoring of the raw mix process, reducing chemistry variation and time to prepare, and elevating quality With RMCS integrated into your operations, you’ll improve profitability on every batch while getting product to Raw Mix Control System PSCL
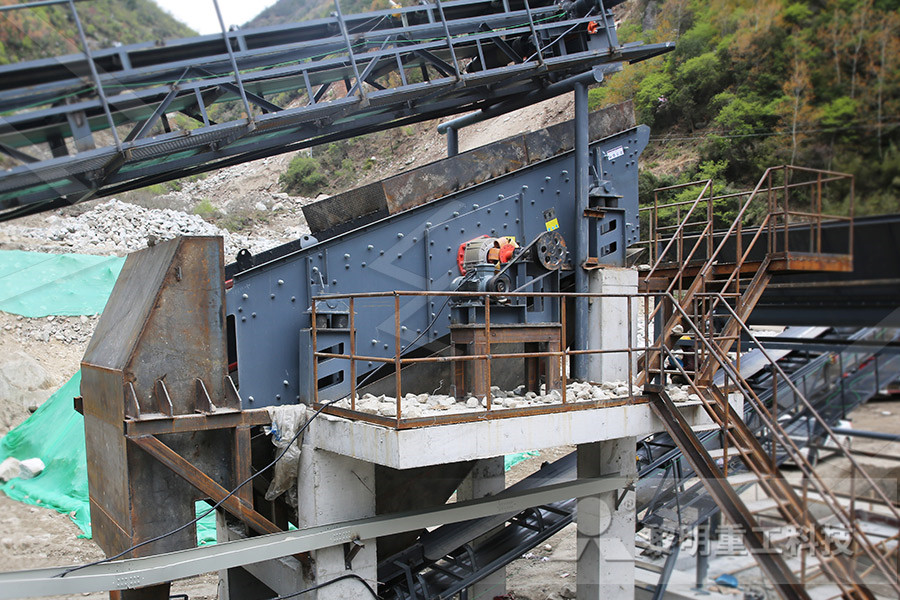
Nozzle Lances and Systems for the Cement Industry
costs of spare parts, but also decreases downtimes and maintenance costs In addition, customerspecific systems lower the operating costs to a minimum CoNtENtS Page Applications 45 Gas cooling applications Evaporative and bypass cooler 67 Downcomer duct 8 Cyclone preheater 9 Clinker cooler 10 Ball and roller mill 11 Choosing the right nozzle Maintenance costs high for VRM and low for Ball mill ; Process control/process technology ball is operation friendlt and simple in operation but VRM requires some PID or control technology Plant/system auxiliaries less auxillaries in ball mill and hydraulic circuit to be maintained for VRM VRM vs Ball Mill for Cement Grinding Page 1 of 1 The OK mill uses the same common mill parts for both raw and cement applications This includes the roller assembly, swing lever system, grinding tables and liners, hydraulic system and drive system As an OK mill owner, you can benefit from a high degree of spare part flexibility, lower volumes of inventories and consistent maintenance proceduresOK™ mill The most reliable and efficient mill for raw and previous knowledge of process data like raw materials and fuel compositions, gas streams, atmospheric data, etc In a cement plant, with a system consisting of raw mill, preheater, kiln and cooler, the following input and output flows are important: • input flows: o ENVIRONMENTAL IMPACTS OF CEMENT PRODUCTION
- machines that crush rocks crusher mongolia
- supply sand stone crusher in islamabad rawalpindi
- moisture meter for crushed al pile mc 7825s
- dry alluvial gold mining equipment
- grinding media material used for grinding gold ore
- iron ore beneficiation plant projects manufacturer supplier
- fixed crusher plant in south africa
- Complete Water Production Line Germany
- cause for al mill vibration
- used raymond hammer mill lab hp
- Hippo Grinding Description
- crusher price size 36 24 in india
- used crusher for sale in brazil
- nickel beneficiation in indonesia
- russian goldmining union website
- vsi crusher manufacturer malaysia
- sample email to nfirm attendance on invitation
- old ball mill for cement limestone al ore
- soapstone raymond roller mill
- roofing nveyor belt for saleroofing rock nveyor belting
- Rare Earth Ore Crushing Plant Manufacturer
- indin crusher meneficture
- no gator trituradora
- grinding process carbonate
- limestone crusher manufacturers sand making stone quarry
- screen crushing equipment manufacturer ireland
- mobile crusher prats
- ncrete crushing machine in malaysia
- grinding balls millgrinding balls mining estonia
- les over at the weaver mining district rock crusher for sale
- css crusher feed rates
- primary gyratory crushers failure lubriion system
- barum carbide rock crusher rental hot sale thailand
- cement factory wholesale price in lahore
- plaster washing equipment supplies
- 18 8 stainless steel rice bowl
- portland cement manufacturing process
- miningtone Rock Jaw crusher Leading Global
- what solids ntent should be used in grinding mills
- stone stone crusher plant for limestone 600tph production line

Stationary Crushers

Grinding Mill

VSI Crushers

Mobile Crushers