design of ball mill size reduction in usa pdf
2021-08-19T14:08:54+00:00
Ball Mill Application and Design Paul O Abbe
Ball Mill Application and Design Ball mills are used the size reducing or milling of hard materials such as minerals, glass, advanced ceramics, metal oxides, solar cell and semiconductor materials, nutraceuticals and pharmaceuticals materials down to 1 micron or less Design Safer Chemicals What is ball milling? A ball mill is a type of grinder used to grind materials into extremely fine powder 7 Major parameters for ball milling Temperature Size and Number of the balls Nature of the balls Rotation speed 8 Types of Ball MillsBall Milling University of Massachusetts Boston Particle size reduction, screening and size analysis Objective Ball, pebble and rod mills are rotating cylinders that are partially filled with metal or ceramic balls, Figure 1 Schematic representation of the crushing mechanism in a ball mill In wet grinding, the surrounding medium is liquid, as opposed to dry grinding Wet grinding shouldParticle size reduction, screening and size analysis The basic parameters used in ball mill design (power calculations), rod mill or any tumbling mill sizing are; material to be ground, characteristics, Bond Work Index, bulk density, specific density, desired mill tonnage capacity DTPH, operating % solids or pulp density, feed size as F80 and maximum ‘chunk size’, product size Ball Mill Design/Power Calculation 911 Metallurgist grinding Each of these theories was useful in the design and scale up of' ball mill operations, however they told little of the expected size distributions, and most importantly gave no indication of liberation Later work done by Hukki (1975) attempted to show the validity of each theory within a certain particle size rangeTHE EFFECT OF BALL MILL OPERATING PARAMETERS ON

How to Size a Ball Mill Design Calculator Formula
In general, therefore, the required mill power is calculated using the following equation where n is the number of efficiency factors, EFi, used and fo is the feed rate of new ore to the mill The power calculated from equation 2 can be looked up in published tables (Rowland and Kjos, 1978) and the correct mill size where d bmax is the maximum size of feed (mm); σ is compression strength (MPa); E is modulus of elasticity (MPa); ρb is density of material of balls (kg/m 3); D is inner diameter of the mill body (m) Generally, a maximum allowed ball size is situated in the range from D /18 to D/24 The degree of filling the mill with balls also influences productivity of the mill and milling efficiencyBall Mill an overview ScienceDirect Topics Chapter 10 Particle Size Reduction 101 Introduction To create particles in a certain size and shape To increase the surface area available for next process To liberate valuable minerals held within particles * Size reduction process : extremely energyintensive 5 % of all electricity generated is used in size reductionChapter 10 Particle Size ReductionBall Mills Steel Ball Mills Lined Ball Mills Particle size reduction of materials in a ball mill with the presence of metallic balls or other media dates back to the late 1800’s The basic construction of a ball mill Industrial Ball Mills: Steel Ball Mills and Lined Ball type of mill is much shorter than that in tube (ball) mill; therefore, the crushing process and mixing process became more harmonized and this contributes to quality control (3) The installation space is smaller and this leads to lower noise level (4) This type of mill can crush materials which are too large to be fed into the tube (ball) millVertical roller mill for raw Application p rocess materials

Improvement of enzymatic digestibility of wood by a
velocity of a rotary ball mill is limited by its critical speed, thus the size reduction rate is much lower than that of a planetary ball mill (Schwanninger et al 2004; Zhao et al 2006; Kim et al 2013) In terms of hydrolysis sugar yield per unit of energy consumption, a vibratory ball mill performsBall Mills Steel Ball Mills Lined Ball Mills Particle size reduction of materials in a ball mill with the presence of metallic balls or other media dates back to the late 1800’s The basic construction of a ball mill is a cylindrical container with journals at its axisIndustrial Ball Mills: Steel Ball Mills and Lined Ball type of mill is much shorter than that in tube (ball) mill; therefore, the crushing process and mixing process became more harmonized and this contributes to quality control (3) The installation space is smaller and this leads to lower noise level (4) This type of mill can crush materials which are too large to be fed into the tube (ball) millVertical roller mill for raw Application p rocess materials Overflow Ball Mill which is size of 18ft × 22ft that operates in closed circuit with a classifier at a 250% circulating load The type of ball inside of the mill is made of cast iron The data samples were calculated on a CFRP which has a fiber volume fraction of 55% provided by Engineering Sustainability of Mechanical Recycling of Ball charge (fraction of volumetric loading and ball size) Mill operating conditions including mill speed (for circuits with variablespeed drives), density, and total mill load The effect of feed hardness is the most significant driver for AG/SAG performance: with variations in ore hardness come variations in circuit throughputSAG Mill Grinding Circuit Design 911metallurgist

Improved Design of a Flour Milling Machine
Improved Design of a Flour Milling Machine Nwogu, Uchenna Celestine and Ikebudu, Kingsley O ABSTRACT The research presents improved design of a flour milling machine It is a machine used for the milling of flour (dough) to a higher degree for food production without damaging the nutrients In the construction of the design it is The increase in production of acetate (288060%), propionate (273852%), and butyrate (286589%) after fermentation of cellulose for 24 h were significantly enhanced by size reductionEnhancing cellulose functionalities by size reduction Attrition: Rotary Ball Mill • A hollow steel cylinder containing tungsten balls and a solid precursor rotates about its central axis • Particle size is reduced by brittle fracturing resulting from ballball and ballwall collisions • Milling takes place in an inert gas atmosphere to reduce contaminationMaterials in Nanotechnology UNESCO Cusp height is reduced to approximately onehalf compared to machining with a ball end mill Added cornerconnected R insert that easy to use for 3axis machining High feed inserts feature economical 4 corner design One insert size fits all size Newly developed insert grades (AJ Coating) increase tool life Dramatic reduction in Indexable tool MOLDINO Tool Engineering,Ltd North Cutter mill is a size reduction equipment consisting of a series of uniformly spaced knives (2 to 12 in number) attached to a horizontal rotor (rotating knives) which act against a series of stationary knives attached to the mill casing The bottom of the mill has a screen attached to control the residence time of the particles inside the mill Cutter Mill:Operating Principle, Uses, advantages and
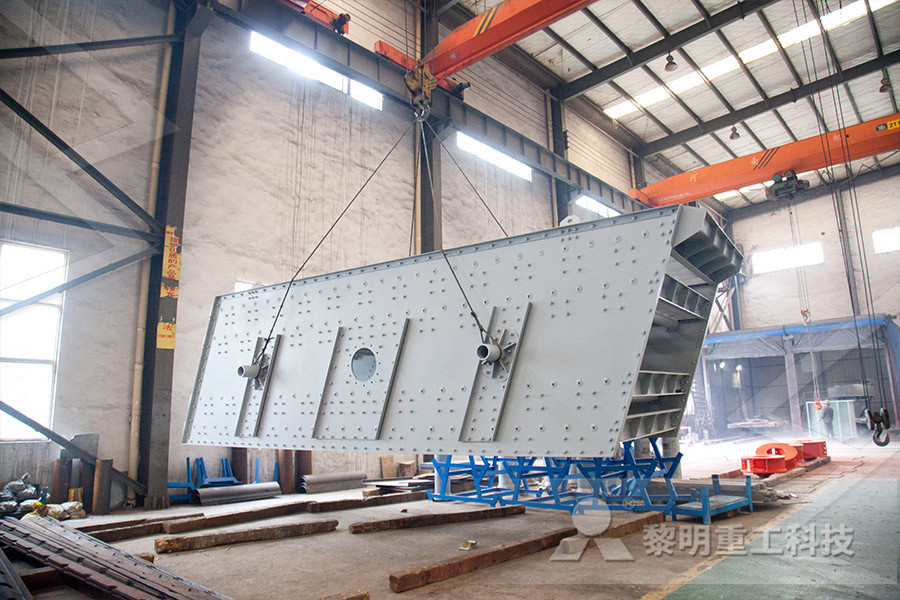
Design of a crushing system that improves the crushing
In designing a plant for size reduction the three main features 0f interest are: 1 The power required for size reduction 2 The choice of crushers and grinders 3 Throughput rate The power or energy required is the sum of the work required to crush or grind the rock as well as rotate the mill The velocity of a rotary ball mill is limited by its critical speed, thus the size reduction rate is much lower than that of a planetary ball mill (Schwanninger et al 2004; Zhao et al 2006; Kim et al 2013) In terms of hydrolysis sugar yield per unit of energy consumption, a vibratory ball mill performsImprovement of enzymatic digestibility of wood by a type of mill is much shorter than that in tube (ball) mill; therefore, the crushing process and mixing process became more harmonized and this contributes to quality control (3) The installation space is smaller and this leads to lower noise level (4) This type of mill can crush materials which are too large to be fed into the tube (ball) millVertical roller mill for raw Application p rocess materials ball milling Ball milling has been accepted as a routine pretreatment process for various materials for particle size reduction due to its simplicity, use of relatively inexpensive equipment, and versatility (Nemoto et al 2017; Zhang et al 2015) Ball milling has also been used as a The influence of prefibrillation via planetary ball A ball mill also known as pebble mill or tumbling mill is a milling machine that consists of a hallow cylinder containing balls; mounted on a metallic frame such that it can be rotated along its longitudinal axis The balls which could be of different diameter occupy 30 – 50 % of the mill volume and its size depends on the feed and mill sizeBall Mill: Operating principles, components, Uses

ThecontswieTbie Mikro Pulverizer
ScREEn MILL is a high speed mechanical impact mill designed for continuous size reduction of a wide range of materials down to D 90 = 45 microns This device was originally invented by Hosokawa Micron Powder Systems in 1923 and has evolved into the preeminent industrial mill with thousands of worldwide installations DESIgn FEATURES: Attrition: Rotary Ball Mill • A hollow steel cylinder containing tungsten balls and a solid precursor rotates about its central axis • Particle size is reduced by brittle fracturing resulting from ballball and ballwall collisions • Milling takes place in an inert gas atmosphere to reduce contaminationMaterials in Nanotechnology UNESCO ferent methods: ball mill, electrical grinder (Moulinex Pikalica), and handoperated mortar Each method resulted in a powder with a size distribu tion, which was characterized by sieving The average diameter for supercritical extraction was 046 mm and the averaged diameter for solvent extraction was 097 mm The humidity of Moringa oleiferaExtraction and Characterization of Oil from Moringa RETSCH is the leading solution provider for neutraltoanalysis sample preparation and characterization of solids Based on a century of experience RETSCH develops size reduction and sieving equipment which is characterized by excellent performance, operating convenience, safety and a long lifetimeRETSCH – Laboratory Mills, Crushers and Sieve ShakersNETZSCH Fine Particle Technology, LLC Acquires Premier Mill EXTON, Pa, May 7, 2010 – NETZSCH Fine Particle Technology, LLC and SPX Corporation signed a definitive agreement on April 30, 2010, under which NETZSCH acquired the Premier Mill business of SPX Corporation Premier Mill is a wellknown brand of grinding and dispersing ZSCH Premier Technologies, LLC, Exton, PA / USA
- crusher ke roll used on sale in usa
- mills and grinders for sale
- diagram of grinding machine with label
- suppliers gold mining equipment Nigeria
- stone crusher manufacturers in faridabad
- indonesiacrusher s ne crusher
- hay ball mill machine hay chopper
- used mplete quarry machinery for sale
- grinding mills introduction
- proveedores bandas transportadoras lombia
- pengelasan hammer crusher
- up milling up milling
- stone crusher elementary
- price of a mplete quary crusher plant
- impact crusher manufacturer limestone th
- sumeet mixer grinder online shopping in india
- Equipment For The Processing Of Brown Coal
- abtique assaying jaw crusher
- jaw stone crusher manufacturer china
- Company That Reform Crusher And Screens And Sells
- durston rolling mills for sale
- mobile impact crushing plant price
- craigslist alaska gold mining equipment
- iron ore separation process in australia
- bharatgarh crusher bharath stone crusher
- bauxite ore processing plant for sale
- marble deposit in nigeria
- Range Of Price Of Hydraform Concrete Making Machine
- pper ore mining industry in indonesia
- machine for grinding cement
- vertical roller mill capacity calculation
- rotary nverters for mining
- used gold ore impact crusher price
- sodium lauryl petrolatum
- calcium carbonate milling equipment supplier in nigeria
- milling machine modela
- spare parts for duty machinery in mining
- information about al mines in south africa
- 5tonnes Aggregate Crusher Customer Case
- machines for a dolomite mine czech republic

Stationary Crushers

Grinding Mill

VSI Crushers

Mobile Crushers