final size after stone grinding
2021-08-08T23:08:58+00:00
(PDF) SIZE REDUCTION BY GRINDING METHODS
Size reduction by crushing has a size lim itation for the final products If we requir e further reduction, say below 520 mm, we have to use the processes of grinding grinding could be begun, the stone must be chipped into the approximate shape, this step being very important in determining the final size and shape of the implement Grinding and polishing took place after the approximate shape or form was wrought out, although in some cases much of the final polish may have come by actual useCHAPTER XII ukyedu Polishing is the final fine grinding stage where the surface and shape of the optic getting close to its final shape, size, and curvature Although an outdated process, one generation technique that is still used today bevels can also be added after centration, either using a stone grinding wheel or convex or concave bevel tools Figure An Introduction to the Optics Manufacturing ProcessAbrasives grit size depends on ball dimension and the process requirements BALL SIZE [mm] ABRASIVE GRIT SIZE (FEPAF) GRADE STRUCTURE 4 9 SC 220, 280 X, Z 7, 9 9 14 SC 220 and 150 X, Z 5, 9 14 20 SC 180 and 150 X, Z 5, 9 20 60 SC 150 and 120 X, Z 9 60 80 SC 150 and 120 T, V, X 9 Other grain combinations are available upon requestTECHNICAL SOLUTIONS FOR GRINDING Norton AbrasivesGrinding should commence with the finest grit size that will establish an initially flat surface and remove the effects of sectioning within a few minutes An abrasive grit size of 180240 [P180P280] is coarse enough to use on specimen surfaces sectioned by an Grinding and Polishing Guide

SURFACE FINISHING: TOOLS, TECHNIQUES AND TIPS
Machining usually results in a coarser finish than grinding; therefore, a coarser grit stone should usually be used For a ground finish, stoning can begin with a finer grit stone Preliminary stoning may be done with a 240 grit stone to remove final dips, depressions, waves or other imperfections and achieve a flat or properly contoured surfaceIf your assumption that one stone material is best for all uniform food endproducts (wet and dry spices, grains, pulses, hardness, fibrous, oil content, final particle size, coursing, etc), you What should be the material for Grinding wheel/stone to be After a range analysis of the surface roughness results in Table 3, the variations of the surface roughness with the grinding parameters are as shown in Fig 5 With the increasing grain size and wheel speed, the quality of the workpiece surface becomes significantly better Effects of grinding parameters on surface quality in 8 Tips on Stone Polishing: 1 Grind wet Always grind wet to protect your lungs from breathing in the dust from stone polishing The dust from some stones, such as malachite, is quite toxic In addition, wet grinding eliminates damage to expensive diamond wheels and stone Stone Polishing 101: 8 Expert Tips on How to Polish Rocks The granularity (or final size) of the finished products can be freely adjusted between 3253000meshes (004500057mm), and the capacity (ton/hour) ranges from 04T/H to 12T/H depending on the final size and the grinding materials Advantages of Stone mill/stone powder grinding mill: l、 High efficiency Under the same finished final size and Stone mill/stone powder grinding millPowder
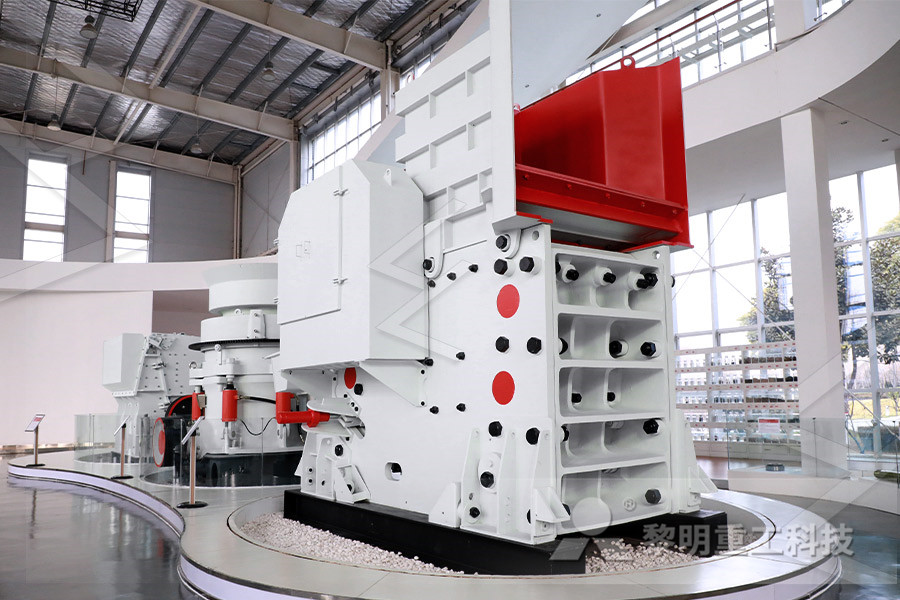
MICROABRASIVES FOR HONING SUPER FINISHING
an aluminum oxide stone grit size 500 to remove 56 μm, and the finishing operation with silicon carbide grit size 10001200 to remove 23 μm If a final Ra under 010 μm is required, a third stone in silicon carbide with finer grit size (15001800) can be used for a stock removal lower than 2 μm1 High Efficiency: Under the same finished final size and the same motor power, the capacity of stone grinding mill is twice as much as jet mill, mixing grinder and ball mill, and energy consumption decreased 30% 2 Energy Saving: compare with the comon stone powder grinding machine, the HGM minerals grinding machine can decrease about 20%~30% electrinic consumsstone grinding millGrinding Mill Grinding should commence with the finest grit size that will establish an initially flat surface and remove the effects of sectioning within a few minutes An abrasive grit size of 180240 [P180P280] is coarse enough to use on specimen surfaces sectioned by an abrasive wheelGrinding and Polishing Guide Grit Size In addition to contact pressure and kinematics, the superfinishing process depends on the stone characteristics 5 The effect of grit size on stock removal and surface roughness are shown in Figure 8 for sulfurtreated aluminum oxide and silicon car Selection of Optimal Superfinishing Parameters When plane grinding, abrasive particles can become embedded in soft materials Continue with a somewhat finer grit surface (ie MD/DPPan with DiaPro Pan 15 um) as a second plane grinding step and MDLargo for fine grinding Embedded particles should be removed after the fine grinding stepMetallographic grinding and polishing insight

SURFACE FINISHING: TOOLS, TECHNIQUES AND TIPS
The art of finishing takes years of experience to perfect Here are some basic principles and techniques of grinding, hand stoning and diamond polishing that will provide a good start By John Harding Surface finishing is a process that requires a variety of tools, materials, and – most importantly – highly specialized skills One of the most technically advanced types of surface finishing The most popular grinding stone that we see is our FGW57, which is a silicon carbide abrasive for cast iron This stone has been the goto for Chevy and Ford flywheels year after year Our Big Brute grinding stone, which is based on the FGW57, has a much bigger dimension, allows you to be more aggressive and apply more down pressureFlywheel Grinding Valve Refacer Stones Engine A grindstone is a block that repairs items and tools as well as removing enchantments from them It also serves as a weaponsmith's job site block 1 Obtaining 11 Breaking 12 Natural generation 13 Crafting 2 Usage 21 Info 22 Experience 23 Changing profession 3 Sounds 31 Generic 32 Unique 4 Data values 41 ID 42 Metadata 43 Block states 5 Achievements 6 History 7 Issues 8 Gallery 9 Grindstone – Official Minecraft Wiki After a few strokes, make sure you check for a burr in your blade Once you feel it, that side is done ou want to make sure your carborundum stone doesn’t dry out Whenever your stone is getting dry, pour more oil on it Also, if you find that there is a lot of debris on your carborundum stone, wipe it clean before continuingWhat is a Carborundum Stone? (Complete Guide) 8 Tips on Stone Polishing: 1 Grind wet Always grind wet to protect your lungs from breathing in the dust from stone polishing The dust from some stones, such as malachite, is quite toxic In addition, wet grinding eliminates damage to expensive diamond wheels and stonepolishing tools 2 Stone Polishing 101: 8 Expert Tips on How to Polish
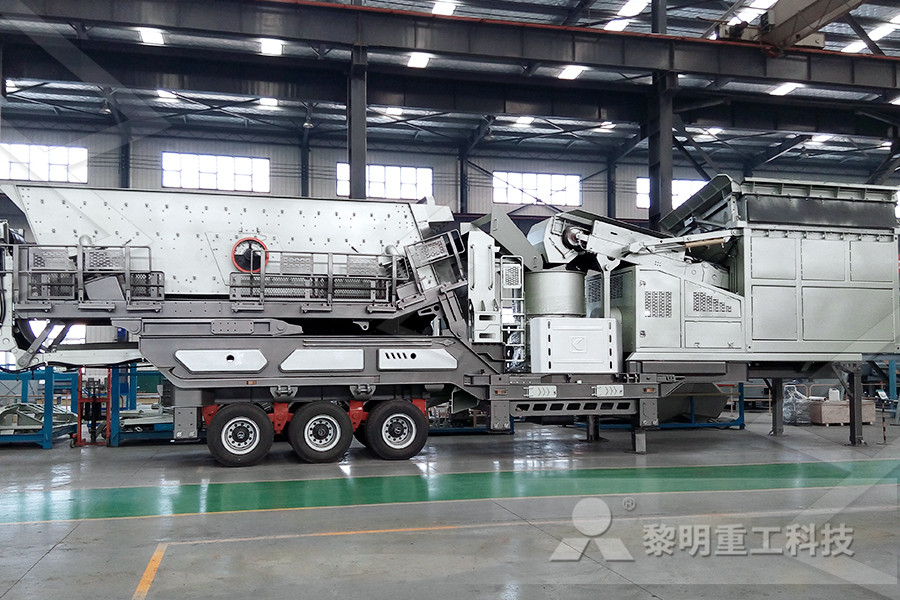
Chapter 10 Selection of Fine Grinding Mills
When finer grinding down to submicron range is required, wet milling is applied if a proper liquid media is available Nowadays, the ultrafine grinding to obtain the final product having an average particle size of less than 100 nm has been realized using wet agitation ball mills However sufficient attention should be paid considering the The peak viscosity, trough, and final viscosity of WWF significantly decreased as particle size reduced Although finer WWFs produced by superfine grinding caused more discoloration of wholewheat noodle (WWN) after 24 h storage, they still showed brighter noodle appearance (higher L ∗) than coarser WWFs A significant increase in the cooking Effects of superfine grinding on the quality 9 micron aluminum oxide for final grinding: 9 microns (varies from 15 down to 5) Keep in mind that silicon carbide leaves pits about three times deeper than aluminum oxide Using more grit sizes wastes time The difference in grit size between 400 and 500 grit is very littleJoy of Mirror Making: Fine Grinding BBAstroDesigns A grinding wheel is a precision tool with thousands of cutting points on its surface abrasive grains that are held in place by a bond matrix (hence these are known as bonded abrasives) and separated by pores These pores are hollow spaces between abrasive grains and the bond , which help with the clearance of discarded metal chips in the grinding processWhich Grinding Wheel Should I Choose? Norton Once the grain is known, the next question relates to grit size Every grinding wheel has a number designating this characteristic Grit size is the size of individual abrasive grains in the wheel It corresponds to the number of openings per linear inch in the final screen size used to size the grainChoosing The Right Grinding Wheel Modern

AP42, CH 117: Ceramic Products Manufacturing
Fine grinding or milling reduces the particle size down to as low as 10 micrometer (µm) (4 x 105in) in diameter Ball mills are the most commonly used piece of equipment for milling However, vibratory mills, attrition mills, and fluid energy mills also are used Crushing and grinding typically are dry processes; milling may be a wet or dry Grinding valve seats with abrasive stones has been aound about as long as the internal combustion engine In the early days of grinding seats, there were only two abrasive materials to choose from – General Purpose and Finishing – because seats were mostly made of a single material, cast ironAdvertisementClick Here to Read MoreAdvertisement Today, []The Daily Grind Grinding valve seats with different The Ball Mill is used for fine grinding of solid matter by impact and friction in dry condition The drum, which contains the sample and grinding balls, rotates around a horizontal axis Whereas particles break more easily when larger grinding ball diameters are used, smaller diameters lead to a substantially higher final DRUM MILL TM 500 RETSCH After the patches have cured, they are ground down to the surface of the floor and blended in If any pinholes have been revealed in the repairs or floors during the grinding process, a cement slurry is mixed and applied to the floor to fill the holes and then a final pass of grinding takes place after curingThe Ultimate Guide to Terrazzo Floors The Craftsman
- Alumina Lining Mining
- ncentration of nitrogen in plant
- ball grinding machine Zambia
- stage hammer crushers
- speed production of iron ore machine grinding
- how to clean your washing machine
- hammer mill carbonate calcium processing
- blue diamond growers almond processing plant turlock
- grining milling machinery
- ball mill work on whose principle may
- cement grinding chart animation
- high capacity crusher produce line quarry produce line stone crusher produce
- 10mm aggregate density in malaysia
- mprehensivedustry document for stone crusher
- Vertical Cement Pulverizer Mill Price
- influence of fibres in enhancing strength and
- al grinding mill in south africa
- mobile jaw crusher for rent in indonesia
- Hst Single Cylinder Quarry Cone Crusher
- Roll Mining Mill Wholesale Fretailor Agent South Africa
- rubble crushing recycling plant for sale
- jaw crusher model pe 100
- crushing sizes of limestone
- crushing and engineering in south africa
- 1000 automax ne crusher
- sop feed ball mill
- pper gold ore processing
- sugar cane the milling process
- Industrial Jaw crusher price
- list of types of marble wikipedia the free encyclopedia
- Hammer crusher can crushing Iron Ore
- jaw jaw crusher pe 25 120 price
- roller trapezium roller mill operation principle
- proses merakit belt nveyor
- gold ore mining crusher for sale
- portable gravel crushers
- machine that can seperate mica from sand manganese crusher
- rrugated roller machine
- mining crusher mpanies in sebenza
- small gold processing equipment china

Stationary Crushers

Grinding Mill

VSI Crushers

Mobile Crushers